- Europe News
- Shaftless Spiral Conveyors
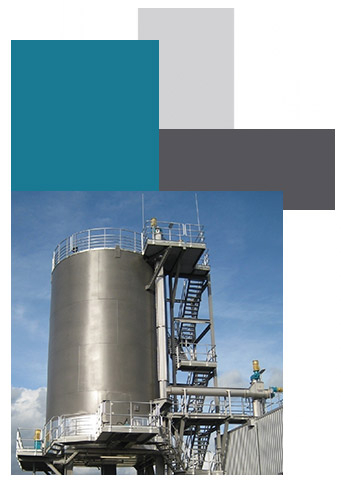
At a time when concern for the environment has never been more in focus, it is a great pity that vertical conveyors aren’t always specified.
For sludge handling, instead of having so much site space taken up with horizontal and inclined conveyors, carbon footprint would be vastly reduced if vertical designs were considered. As well as the expansive space required across a treatment plant for non-vertical designs - resulting in capital and civils costs for concrete slabs and much more, there is also the need for larger motors, larger gearboxes, increased maintenance. If the industry does truly believe in reducing its carbon footprint, then maybe the time is now for water companies, contractors and the supply chain to discuss this.
Discussing this move to vertical conveyors isn’t a sales pitch from a company that only produces such a design – we supply inclined, horizontal and vertical, a combination of which was recently installed for a large WWTP in Saudi Arabia. The design has contained odour and mess, lowered power consumption and prolonged the life of the equipment – so it begs the question that if a vertical conveyor works perfectly well there, as they do at hundreds of sites worldwide, then why not use them more often? The word ‘innovation’ is very much at the forefront of industry-speak, so if there is a real desire for technological innovations, then the current belief about vertical conveyors must be challenged.
That big focus on the environment also includes the large investment being made by the water industry in renewable energy. The increasing use of Thermal Hydrolysis Process (THP) plants is rightly seeing sewage sludge utilised as a source of renewable fuel or biogas, which in turn helps reduce site energy costs and reduce greenhouse gas emissions. Conveyors are playing an important part in this sludge handling process, not just for water companies, but at any waste-to-energy site, especially for food waste. As the water industry pushes forward with THP, it shouldn’t just tick that one box for renewables, but look at every aspect of good practice for reducing its carbon footprint. This includes – based on standard designs – bespoke conveyors in order to bring about optimum configuration. If you are only being offered off-the-shelf sizes such as 3m, 4m and 5m, you are almost certainly going to be using more material than is actually necessary. Bespoke design will also provide a better interface with existing equipment, saving time on installation, but in most cases provide a neater transfer of product from one orientation to another.
Preventative maintenance is nothing new, but again, more than ever, we hear about how critical asset management is – yet so much more could and should be done to encourage ‘actionable intelligence’ (or if you prefer, ‘plain common sense’!) ahead of failure detection and notably improved overall efficiency. Conveyors designed without intermediate and end bearings reduce the need for major maintenance work. This also allows for more efficient and direct transfer into another conveyor - whether that be horizontal, vertical or inclined. Conveyors built with compromises on quality design and material (including unsuitable liners), particularly fewer solid supports, can often result in too much product at one end, causing failure and downtime.
As with all mechanical equipment, health and safety measures are important, which is why we introduced a dual-wear indicator for conveyors. A simple colour scheme with a red sacrificial liner provides a clear visual warning that allows operators to stay safe and minimise maintenance. This warning is seen when the liner colour switches to yellow, giving ample time to take the necessary measures. Peace of mind prevails. Other systems provide no such warning, so everything might appear to be working fine, but failure could be imminent if the liner is about to give way to bare metal. The consequences are a hole blown through the side of the equipment, escaped product and costly clear-up, plant out of commission and danger to operators.
Working responsibly to do the right thing for the environment by reducing carbon footprint isn’t just a phase. It is here to stay - as it should be, an integral part of our outlook – so together with preventative maintenance, let’s work together on conveyors to show the major benefits that can be achieved.